A una decina d’anni dal nostro primo incontro siamo tornati a trovarlo per cercare di capire come mai avesse scelto di fare entrare una macchina che non fosse stata progettata da lui in una delle sue fabbriche…
Se non è un genio poco ci manca. Silvio Pedrotti è un tecnico abilissimo, con una storia e una serie di esperienze che fanno pensare che abbia vissuto più di una vita. Non è facile neanche tenere il conto di tutto ciò che ha fatto a partire dal 1987, quando mise a punto con un amico quello che potrebbe essere definito il primo software per la produzione di serramenti. Lui – figlio di un muratore ma perito meccanico per formazione che a un certo punto sceglie di lavorare il legno – si è perfino divertito a fare qualche “softwarino”, come li chiama lui, con quelle calcolatrici programmabili che certamente qualcuno dei nostri lettori ricorderà.
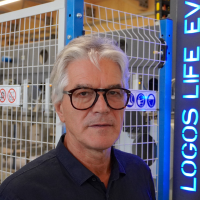
Silvio Pedrotti
“La mia formazione da perito meccanico mi ha sempre portato a rispettare tutti i materiali, ma il legno è il più intelligente: si può coltivare e quando cresce lo si usa per fare mille cose belle. Si può lavorare senza bisogno di tantissima energia e, a parità di massa, regge come l’acciaio! Me ne sono innamorato da giovanissimo e ho cominciato ad averci a che fare con mio papà e i miei zii, muratori nella bella stagione – dalla Settimana santa alla Festa dei Santi – e poi in letargo come gli orsi, a riparare attrezzi, a costruire qualche mobiletto in una stanza adibita a piccola falegnameria. Non c’era la televisione e dopocena mi mettevo di fianco a lui per costruire qualche oggetto, magari un giocattolo per me e i miei fratelli…”.
Comincia così la nostra piacevolissima chiacchierata con Silvio Pedrotti che, quando viene il momento, sceglie di studiare meccanica: le moto, i trattori, le falciatrici di una terra fortemente contadina erano un richiamo troppo forte, ma il legno non ci ha messo molto a far sentire il suo richiamo e il militare gli ha fatto presto capire quale fosse la sua strada e che di padroni non ne avrebbe mai avuti. I primi clienti gli danno fiducia e Pedrotti comincia a far finestre, prima per la sua casa di Cavedine, uno splendido angolo di Trentino, e a poco a poco per altri. Le cose cominciano a ingranare e tutta la famiglia viene coinvolta: prima il papà Giovanni, poi i sui fratelli Michele, enologo, e Nicola, chef: tutti a fare i falegnami!
Nel 1985 il primo laboratorio, sempre più grande, dove a un certo punto si comincia anche a produrre mobili. E poi, attraverso alterne vicende, si arriva alla Essepi (acronimo di Silvio Pedrotti) di oggi, organizzata in quattro capannoni, ciascuno con una funzione specifica: lo spazio per la fabbrica di serramenti, un secondo edificio dove nel 2012 Pedrotti inizia a produrre X-lam, un terzo completamente dedicato alla selezione delle tavole per la produzione di legno strutturale e il quarto, ultimato pochi mesi fa, che ospita la nuova, grande linea automatica firmata dalla Working Process di Niviano di Rivergaro (Piacenza).
“Il progetto X-Lam, che oggi rappresenta un buon 50mper cento del nostro fatturato, nasce dall’idea di offrire al mercato una parete davvero completa, con tanto di serramenti. Elementi pronti per essere velocemente montati in cantiere, una opportunità molto apprezzata in alcuni Paesi stranieri e ancora purtroppo poco conosciuta in Italia, ma confido di far cambiare idea a molti nei prossimi anni”.
E non facciamo fatica a credergli, perchè Pedrotti ha le idee chiare, molto chiare, come quando si è costruito le macchine per attrezzare i quattromila metri di capannone per l’X-Lam… che, a dire il vero, doveva essere uno spazio nel quale produrre macchine per il legno, per la lavorazione e l’assemblaggio di serramenti pre-verniciati. Già, perchè lui è sempre stato convinto che la pur vasta offerta nazionale e internazionale non fosse esattamente ciò che a lui serviva. E se in Trentino ci fosse stata una più diffusa vocazione per la meccanica il presente sarebbe certamente stato diverso per Silvio Pedrotti, per quanto – grazie anche alla sua formazione da perito meccanico – si sia sempre progettato e costruito le macchine di cui aveva ed ha bisogno. Con una eccezione: Working Process.
“È vero: ho tenuto duro fino al 2014, quando Massimo Schiavetta, che conosco da una vita, mi ha convito ad andare a vedere le sue macchine all’opera. Fu allora che mi resi conto che tecnologia, la filosofia, il “pensiero” che da sempre inseguivo era realizzabile con le macchine che costruiva il mio amico Massimo con la sua squadra, una azienda che da allora ha continuato a crescere da tutti i punti di vista, soprattutto della intelligenza e della efficacia delle macchine per la produzione di serramenti pre-finiti.
Ricordo come se fosse oggi la prima macchina che venne a installare qui da me con i suoi tecnici, un centro di lavoro usato e ricondizionato che è stato il cuore della nostra produzione fino a pochi mesi fa, quando abbiamo scelto di compiere un altro, importante passo in avanti, acquistando un centro di lavoro particolarmente “intelligente” inserito in una linea automatica con magazzini per il carico e lo scarico.
Ci siamo ritrovati a lavorare con una tecnologia migliore, potendo disporre di più teste operatrici e soprattutto di una meccanica e una elettronica più sofisticate, grazie alle quali realizzare cicli di lavoro ottimizzati sulla base delle nostre distinte, lavorando elementi che vengono piallati e avviati alle fasi successive da sistemi automatici, che vengono perfino vaporizzati perchè abbiano la giusta umidità per essere trasformati nel miglior modo possibile e poi messi a disposizione dell’operatore in un magazzino dedicato, perfettamente organizzati per commessa, pronti per la verniciatura.
In questo “percorso” abbiamo ritrovato le idee che abbiamo inseguito per anni, il processo che abbiamo sempre applicato ma che questa volta era affidato a un sistema evoluto, progettato e realizzato da una realtà che ha maturato una grande esperienza in questo comparto. Una macchina, che grazie ai magazzini che ho già ricordato, ci permette di produrre anche senza presidio, oltre i normali turni di lavoro.
Una sola persona controlla tutta la linea, con una gestione in gran parte delegata all’ufficio tecnico che trasmette i programmi da eseguire dopo aver sviscerato tutti gli aspetti o le eventuali specificità o “difficoltà” della commessa. Una “pre-organizzazione” che permette all’operatore di concentrarsi sui suoi compiti, perchè rimane una presenza importante quando si vuole fare qualità: per quanto il centro di lavoro risponda alla forte diminuzione delle professionalità e delle competenze disponibili, un bravo falegname resta un valore aggiunto importantissimo per una azienda”.
Non deve essere stato facile per lei accettare una “macchina estranea” in quello che potremmo definire il suo mondo…
“Quando ci si ritrova per le mani qualcosa di valore bisogna saperlo riconoscere e farne una strumento della propria visione. Quando abbiamo scelto la nostra “Logos Life Evo 3555 IMML UML”, un nome non certo semplice da ricordare, abbiamo deciso di costruirci attorno un nuovo capannone, così da non interferire sui tempi della produzione, portata avanti dalla nostra vecchia “Working Process”.
In tre settimane abbiamo costruito la struttura in X-Lam, un grande spazio per metà dedicato alla linea di prozuone e l’altra metà allo stoccaggio degli elementi pronti per essere messi in macchina.
Oggi tutta la nostra produzione di serramenti passa da questa linea, da cui escono elementi in legno che mandiamo direttamente alla verniciatura, senza alcuna levigatura intermedia. Una precisione assoluta che è il risultato della scelta di afferrare il pezzo con un sistema di pinze per poterlo lavorare su tutte e sei le sue facce senza mai lasciarlo, garantendo dunque precisione e ortogonalità assolute, lontane anni luce da quello che si poteva ottenere prendendo e riprendendo ogni pezzo almeno una decina di volte prima di completarlo”.
Signor Pedrotti, il mondo del serramento è cambiato così tanto?
“Assolutamente sì. E sono cambiati i “modelli” di serramento: non esiste più solo la finestra a una o due ante, ma c’è tutto un mondo di forme e di funzioni, dagli archi ai trapezi, dagli alzanti agli scorrevoli fino a sistemi vetrati che arrivano a pesare diversi quintali! Un prodotto che deve nascere da mani competenti, realizzato con macchine e attrezzature idonee…
Il serramento è diventato più complesso ed è sempre più vicino all’essere una parte dell’arredo, caricato di forti valori estetici e con prestazioni, regolate da norme internazionali, che sono cento volte migliori rispetto anche a solo una decina di anni fa.
Prodotti complessi, che comportano una spesa significativa per il committente se si vuole la qualità, che devono essere necessariamente collocate in un mercato vicino per la loro peculiarità, per la necessità che siano montate in modo corretto, con la stessa professionalità con cui sono state costruite.
In questo, come le dicevo, la scelta di inserirle nelle nostre pareti in X-Lam qui in fabbrica e di spedire il “pacchetto completo” è una garanzia di qualità del sistema nel suo insieme, perchè si evita tutto ciò che ruota attorno a una più o meno corretta installazione. Non le nascondo che a montare i serramenti che vendiamo in un raggio di 150, 200 chilometri preferiamo mandare le nostre squadre”.
a cura di Luca Rossetti
essepi.it
working-process.com
La “Logos Life Evo 355 Imml Uml” in breve
Il centro di lavoro installato presso Essepi è un “Logos Life Evo” dotato di cinque teste operatrici, tutte con elettromandrino idraulico e cambio utensili con fissaggio “Hsk 63”; teste che possono lavorare senza alcun problema con utensili fino a 15 chilogrammi di peso, prelevati da un magazzino da 248 posizioni.
Una macchina dotata di una serie di pinze indipendenti a doppia presa, sia sul lato destro che sinistro, in modo da poter lavorare entrambi i profili, oltre ad effettuare tutte le lavorazioni di fora-fresatura.
La soluzione scelta da Essepi può lavorare elementi con lunghezze fino a 5.500 millimetri, larghezze fino a 240 e una altezza fino a 150 millimetri, dai quali si possono ottenere anche pezzi lunghi solo 120 millimetri, ottenendo più elementi dallo stesso profilo.
“Una linea automatica potente e al tempo stesso fortemente flessibile – ci spiega Filippo Schegginetti, consigliere delegato e responsabile marketing e comunicazione di Working Process – che, oltre al nostro centro di lavoro, riunisce diverse macchine: scorniciatrice quattro lati, troncatrice, levigatrice e due magazzini intelligenti, uno per il carico e l’altro per lo scarico degli elementi in lavorazione. Un progetto nato per garantire un’ottima produttività, attorno ai 400 elementi per turno, anche nel caso ci sia la necessità di lavorare serramenti molto diversi fra loro, una potenza in gran parte dovuta alla presenza del nostro magazzino “IMML- Intelligent Magazine Multi Level”, progettato e prodotto a partire dal 2010 e oramai parte di oltre un centinaio di nostre referenze in tutto il mondo, grazie al quale l’intero ciclo può essere programmato nel modo più efficace ed efficiente.
Una macchina che monta gli stessi aggregati ed è costruita con gli stessi elementi e secondo gli stessi standard delle “sorelle maggiori” ma anche delle nostre soluzioni più “entry level”, perchè la nostra filosofia è fornire sempre le tecnologie più performanti e innovative, calibrate sui volumi di prodotto che si intende realizzare”.