Ten years after our first meeting, we came back to understand why he decided to equip one of his factories with a machine he had not designed.
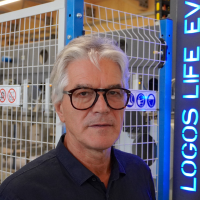
Silvio Pedrotti
If he’s not a genius, he’s close to. Silvio Pedrotti is a highly skilled engineer, with a story and a pack of experience that make you think he has lived more than once. It’s not easy to tell everything he has done since 1987, when he created what can be considered the first software for window manufacturing, together with a friend. The son of a bricklayer, he studied as a mechanical engineer and then decided to process wood. He even enjoyed creating some “little software”, as he calls it, with those programmable calculators some of our readers might remember.
“My mechanical engineer education always helped me respect all materials, but wood is the most intelligent: it can be cultivated, and when it grows, you can use it to make thousands of beautiful items. You can process it with not so much energy, and given the same mass, it is as strong as steel! I have been fond of wood since I was young, and I started to deal with it with my father and uncles, who worked as bricklayers in the warm season (from Easter to Halloween) and then went into hibernation like bears, repairing tools, making some cabinets in a small workshop inside their home. There was no television, so after dinner, I sat next to him to build some items, maybe a toy for me and my brothers…”.
In 1985 they created the first workshop, which was gradually expanded, until they started to manufacture furniture. And then, more things happened, until the creation of today’s Essepi (the spelled-out acronym of Silvio Pedrotti), with four halls, each with a specific function: one for the window factory, one where Pedrotti started to produce X-lam in 2012, one entirely dedicated to board selection of glulam timber, and one, completed a few months ago, hosting the new big automated line designed by Working Process from Niviano di Rivergaro (Piacenza).
“The X-Lam project, currently accounting for 50 percent of our revenues, originated from the idea of delivering a complete wall, including windows. These elements are ready to be installed in the construction site, which is highly appreciated in a few countries, but unfortunately, still not so popular in Italy; however, I am confident that many people will change their mind in the coming years”.
And we believe him, because Pedrotti has a very clear vision, just like when he manufactured his own machines to equip four-thousand-square-meter X-Lam workshop. Actually, this was going to be a facility for the production of woodworking machinery, for processing and assembling pre-painted windows. Pedrotti has always believed that, despite an extensive Italian and international offer, that was not exactly what he needed. And if the Trentino region had had a stronger vocation for mechanical engineering, the present time would have been different for Silvio Pedrotti, although he has always designed and built the machines he needed, leveraging his education as a mechanical engineer. With one exception: Working Process.
“That’s true: I resisted until 2014, when Massimo Schiavetta, a long-time friend, invited me to go and see his machines in operation. That’s when I realized that the technology, the philosophy, the “concept” I had always pursued could be achieved with the machines built by my friend Massimo and his team, a company that has been growing under every aspect since then, especially for the intelligence and effectiveness of their machines for pre-finished window production.
I still remember when he came to install the first machine with his engineers, it was a reconditioned machining center that represented the heart of our production until few months ago, when we decided to make another step forward, acquiring a very “smart” machining center embedded into an automated line with loading and unloading magazines.
We stared to work with a better technology, with more operating heads, and most of all, more sophisticated mechanical and electronic features, that enable optimized workflows based on our bills of materials, processing elements that are planed and transferred to downstream stages by automated systems; the parts also go through a steaming stage to ensure the proper level of moisture for subsequent processing, then they are delivered to the operator in a dedicated warehouse, perfectly organized by order, ready to be painted.
In this “sequence”, we have found the ideas we had been pursuing for years, the same process we had always applied, but now entrusted to an advanced system, designed and created by an organization with longstanding experience in this industry. Thanks to the storage systems I mentioned, this machine can also work unattended beyond the traditional working shifts.
One person operates the entire line, while management is mostly delegated to the technical department that send the working programs after analyzing all aspects and possible peculiarities or “challenges” of each order. This “preliminary organization” allows the operator to focus on his tasks, as humans are essential if you want to offer high quality: although a machining center compensates for the lack of professional skills and expert workers, a good joiner is still a valuable resource for a company”.
It must not have been easy for you to accept an “external machine” into your world…
“When you come across a valuable solution, you must recognize it and leverage it for your vision. When we chose our “Logos Life Evo 3555 IMML UML”, definitely a tough name to remember, we decided to build a new hall around it, to avoid interfering with the production schedule of our old “Working Process”.
In three weeks, we build the X-Lam structure, a large space where one half is dedicated to the production line, and one half to the storage of ready parts to be fed into the machine.
Today, our window production entirely flows through this line, which outputs wooden parts that are sent directly to painting, with no intermediate sanding. This absolute accuracy is the result of the decision to use a gripper system to seize the parts and work them on all six faces without ever releasing them, thus ensuring full accuracy and orthogonality, totally different from what you could achieve when each part had to be reworked at least ten times before completing it”.
by Luca Rossetti
essepi.it
working-process.com
“Logos Life Evo 355 Imml Uml” in pills
The machining center installed at Essepi is a “Logos Life Evo 3555 IMML UML” model with five operating heads, all equipped with power spindle with hydraulic tool holder, automatic tool changer and “Hsk 63E” locking system; the heads can operate smoothly with tools up to a weight of 15 kilos, picked from a 248-position magazine.
The machine features a set of independent grippers with right-side and left-side grip, so that both profiles can be machined and all tenoning, drilling and milling operations executed.
The solution adopted by Essepi can process elements up to 5,500 millimeter long, 240 mm wide and 150 millimeter high, producing parts as short as 120 millimeters, all with the same profile or even with different profiles from each other.
“It’s a powerful and highly flexible automated line” – said Filippo Schegginetti, managing director and marketing and communication manager at Working Process – which incorporates several machines beside our center: four-side router, cut-off saw, sanding machine and two intelligent magazines, one for loading and one for unloading the workpieces.
This system was designed to offer high productivity, approximately 400/450 different elements per shift, even when very different parts must be processed; such capability is supported by our “IMML- Intelligent Magazine Multi Level”, designed and manufactured since 2010 and currently installed at more than one hundred customers around the world, allowing to program the entire cycle in the most effective and efficient way.
This machine features the same aggregates and is built using the same elements and standards of its “bigger sisters” as well as our entry-level solutions, as our philosophy is to provide always the most performing and innovative technologies, tuned to the product volumes you must produce”.