Parte da questa sua considerazione il nostro incontro con Edmondo Caspani, operation manager della Porro di Montesolaro, in provincia di Como, dove siamo andati a vedere all’opera uno splendido impianto progettato e realizzato dalla Stema di Brenna.
Non è facile far convivere la profonda anima artigianale che da sempre contraddistingue Porro, uno dei pochi sinonimi rimasti di qualità artigianale “made in Brianza”, con la necessità di misurarsi in un mercato sempre più complesso. “E per poterlo fare c’è solo un modo: fare in modo che le persone in produzione, quelle che lavorano negli uffici e le tecnologie “parlino” fra loro”. Non ha dubbi Edmondo Caspani, che torniamo a trovare con grande piacere, a una decina d’anni dal nostro primo incontro, perchè conversare con lui di tecnologie significa cogliere perfettamente e completamente cosa si prova a stare dall’altra parte della barricata, quali sono le necessità, le attese e anche le speranze di chi si misura con le soluzioni più innovative sapendo che il fine è permettere all’“organismo azienda” di esprimersi al meglio, ad ogni livello.
“L’impegno mio e di tanti altri qui in Porro è raggiungere il mix ideale nella collaborazione fra persone, strumenti e risorse”, ci dice Caspani. “Anche per questo abbiamo sempre investito per mantenere aggiornato il nostro parco macchine, incrementando la nostra flessibilità, indubbiamente uno dei nostri valori più importanti, ciò che ci ha sempre contraddistinto e – in fondo – permesso di continuare a essere degli artigiani in grado di fornire mobili su misura, senza alcun limite. Facciamo con macchine avanzatissime quello che avrebbero potuto fare solo dei maestri falegnami ed è in questo che credo si possa riassumere cosa è oggi Porro: una realtà che propone una qualità altissima grazie all’aver saputo trasmettere, trasformare il proprio sapere artigiano in una organizzazione moderna, complessa, efficace. Continuiamo a gestire venti diverse tipologie di legno, continuiamo ad assumere falegnami convinti che il nostro – per quanto fortunatamente fatto con macchine più moderne – sia sempre un lavoro che richiede passione, competenza, oserei dire perfino affetto… ragazzi che incontriamo nelle scuole di formazione e invitiamo a venirci a trovare, accorgendoci del loro stupore quando vedono una azienda organizzata, moderna, efficace ma dove il legno rimane comunque al centro del nostro fare, del nostro essere”.
“Con Stema ci siamo trovati molto bene, perché ci hanno costruito un impianto che abbiamo progettato insieme, perchè rispondesse perfettamente alle nostre necessità e al nostro modo di lavorare, di intendere la precisione e la qualità. Credo che il progetto originario sia stato rivisto mille volte per arrivare a una soluzione finale che ci ha risolto non solo tutti i problemi di foratura, ma ci permette di effettuare molte altre lavorazioni, prime fra tutte la realizzazione delle fresature necessarie per collocare i componenti per l’elettrificazione dei nostri armadi lavorando molto spesso con spessori limitati, aggiungendo così nuove e apprezzatissime funzioni ma sempre con quell’eleganza che è la cifra dello stile Porro. Il tutto su una linea sola linea, non solo riducendo al minimo la manipolazione degli elementi ed eliminando così tutta una serie di rischi, ma concentrando tutte le lavorazioni, dalla fresatura all’inserimento della ferramenta, ottenendo la precisione assoluta…”.
Una sfida enorme per una realtà come la vostra…
“… che ogni giorno realizza 800 elementi per turno, uno diverso dall’altro. Numeri che possono anche sembrare “contenuti”, ma tenga presente che i nostri arredi nascono da sette melaminici diversi, 30 colori, 20 essenze e che tutto questo può essere combinato come il cliente desidera. Non solo: in Porro si lavora su progetto, dunque non c’è la possibilità di fare stock o di avere un magazzino di semilavorati: ogni pezzo è unico, fatto per essere collocato in una specifica configurazione d’arredo: lavoriamo “lotto uno”, come si dice, oramai da più di un decennio”.
“Siamo abituati a risolvere le complessità piuttosto che pensare a produrre per grandi numeri”, interviene Fabio Porro, contitolare dell’azienda che incontriamo durante la nostra visita. “Potremmo produrre molto di più con le nostre macchine e la nostra organizzazione, ma noi abbiamo scelto di usare le nostre tecnologie per continuare a fare il “su misura”, senza mai negare la nostra vocazione per la fascia alta del mercato. I nostri nonni ci hanno insegnato a “lavorare bene” e la qualità è per noi una questione di abitudine, qualcosa che abbiamo dentro: non sapremmo lavorare diversamente, convinti che la Brianza abbia ancora valori importantissimi da esprimere, un territorio diventato nei decenni un efficiente distretto industriale ben integrato e che – superata la sfida del passaggio generazionale – rappresenta un terreno fertile non solo per quanto riguarda il mobile in legno, ma anche per il metallo e altri materiali”.
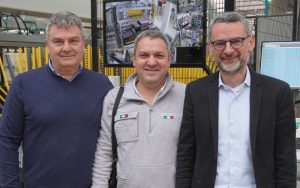
Da sinistra: Giovanni Porro, Enrico Citterio ed Edmondo Caspani
“E per raggiungere questi risultati – prosegue Fabio Porro – bisogna mantenersi estremamente flessibili, facendo praticamente tutto al nostro interno, così da avere la certezza della qualità assoluta. Questo significa investire per attrezzare al meglio ogni area della nostra azienda, dalla sezionatura alla verniciatura, dalle operazioni di fora-inserimento all’imballaggio finale.
Non le nascondo che, nonostante in Porro si sia scelto il meglio di ogni attrezzatura, non è sempre facile conciliare la qualità che perseguiamo con “tempi di attraversamento” che siano i più brevi possibili. Noi abbiamo scelto la nostra ricetta, coscienti che ci sono limiti da non superare, altrimenti si deve necessariamente smettere di essere sè stessi, spostando l’asse dell’impresa verso l’industria e lasciandosi alle spalle quello che si è sempre stati. E in Porro non siamo disposti ad accettarlo”.
“Tornando a parlare della linea realizzata per noi da Stema: all’inizio pensavamo a qualcosa che ci liberasse da ogni problema, una sorta di bacchetta magica che rendesse tutto immedi to e semplice”, riprende Edmondo Caspani. “Non ci è voluto molto per comprendere con loro che se si vogliono assolutamente raggiungere certi risultati si rischia di ritrovarsi per le mani una tecnologia estremamente rigida. È stato così che abbiamo compreso come la soluzione giusta per noi fosse qualcosa che aumentasse la nostra produttività ma al tempo stesso mantenesse una “razionale semplicità” d’uso e soprattutto ci permetta di guardare ai possibili sviluppi dei nostri prodotti con una certa serenità.
Una linea, in altre parole, che ci potrà aiutare anche su strade nuove in un futuro che potrebbe essere poi non tanto lontano, che ci accompagni nella continua evoluzione di un prodotto che nasce e vive delle sollecitazioni di clienti sempre più esigenti, che in ogni angolo del mondo cercano una composizione, un arredo, un ambiente che li faccia sentire a proprio agio, che sia esattamente quanto avevano immaginato per la propria casa…”.
Dunque una scelta tecnologica figlia di molteplici genitori, se ci passa la definizione…
“Assolutamente sì. Come le dicevo oggi lo stile, la qualità, una richiesta di personalizzazione sempre più esasperata portano ad arredi più complessi con i quali tutto il “sistema azienda” deve sapersi confrontare, potendo disporre degli strumenti, della mentalità, dei sistemi gestionali e organizzativi necessari.
La bellezza della nuova linea Stema nasce proprio da tutto questo e ci permette di inserire in linea un pannello – corredato dal bar code con tutte le informazioni necessarie – per poter scaricare, in pochi secondi, un elemento finito ed esattamente come lo abbiamo progettato. Può sembrare banale, ma le garantisco che non è così. Per ottenere ciò che ci eravamo prefissati abbiamo dovuto trovare il giusto equilibrio e unire le forze di quattro macchine: la prima capace di forare e pantografare i bordi secondo qualsiasi schema, a tutti gli effetti un centro di lavoro a controllo numerico; la seconda di eseguire su una facciata tutte le forature e gli inserimenti delle bussole e degli elementi che restano “a filo” e sono dunque più difficili da posizionare manualmente. La terza ripete sostanzialmente le stesse operazioni sull’altra facciata, dopo che il pezzo è stato girato, mentre la quarta esegue ogni operazione necessaria sui lati corti, che si tratti di spine, giunti, reggi-ripiano e di tutte quelle lavorazioni che rappresentano una certa sfida se devono essere fatte manualmente. In ultimo un particolare di cui siamo molto orgogliosi, un sistema laser che codifica, scrive su ogni elemento il codice che lo contraddistibgue, una matricola che lo rende unico, irripetibile e ovviamente tracciabile”.
“Per noi di Stema è stata una gran bella sfida”, ci racconta Enrico Citterio, contitolare dell’azienda di Brenna. “Ci siamo confrontati a lungo con la proprietà, i vertici, i responsabili di Porro per immaginare quale potesse essere la soluzione giusta. E di cambiamenti ne abbiamo fatti, insieme, davvero molti: ricordo, solo per fare un esempio, che nella prima configurazione avevamo addirittura previsto quattro pantografi fissi per raggiungere certi risultati, ma poi abbiamo convenuto che avremmo potuto ottenere un risultato simile affidandoci a un “cambio utensili” che lavorasse su un unico centro secondo determinate impostazioni. E la cosa è piaciuta in Porro, in questo scambio continuo di richieste, di idee e di proposte che hanno poi portato alla linea che – lo devo ammettere – oggi è anche per noi motivo di orgoglio.
Abbiamo lavorato in modo concreto stimolati a trovare soluzioni che non solo rispondessero alle specifiche richieste, ma che lasciassero spazio alle possibili evoluzioni future.
Da qui la scelta di configurare una macchina che avesse una lunghezza adeguata – una quarantina di metri, sessanta se si aggiunge lo spazio dedicato al montaggio eseguito dagli operatori – per rispondere non solo alle necessità fisiche e strutturali di una configurazione indubbiamente molto “ricca”, ma anche per rendere semplice qualsiasi intervento, compresa la possibilità di aggiungere nuovi aggregati in futuro per creare nuove opportunità sul prodotto finito.
Il tutto gestito da remoto, con una serie di telecamere che permettono di monitorare ogni passaggio con la massima tranquillità”.
a cura di Luca Rossetti
porro.com
stemasrl.eu
LA LINEA STEMA per PORRO
Il primo elemento è il caricatore che preleva dalla catasta mista dei pannelli preparati dal reparto di sezionatura ogni singolo elemento e lo avvia al controllo e alla misurazione automatica prima dell’inserimento nella linea vera e propria.
C’è un secondo sistema di carico, ovvero un “riccio” che provvede ad avviare alla lavorazione “lotto uno” anche pannelli speciali, fuori misura o riprese che vengono inseriti senza alcun problema nel flusso della programmazione.
La linea Stema – perfettamente modulare, come tradizione del costruttore brianzolo, per poter gestire al meglio i carichi di lavoro – è composta da due “Grafias C” che provvedono alle lavorazioni sulle due facce del pannello, precedute da un pantografo passante “Grafias V”, realizzato appositamente per Porro, e da una “Mizar” dedicata alla foratura e all’inserimento. Complessivamente sono oltre 80 gli assi controllati, in una linea dove i sistemi di aspirazione e la pulizia – fondamentali per la qualità finale del pezzo in lavorazione – si affiancano a una logica di linea che consente di raggiungere ottimi livelli produttivi ma soprattutto la qualità e di “cura” imposto dagli standard Porro.